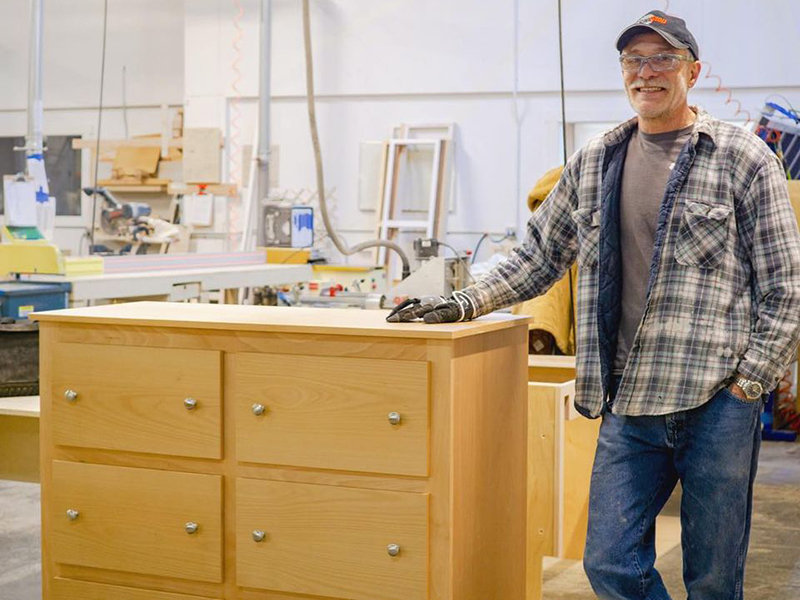
Tackling Toxics: How partnerships produced success at Founder’s Choice
Founder’s Choice Cabinets, a manufacturer based in Tacoma, wanted to do something to help the environment as well as improve their business practices. By turning to Ecology, it not only reduced its environmental impact, but achieved stellar cost savings as well.
Founder’s Choice — a family-owned company that manufactures a variety of custom kitchen and bath cabinetry, and miscellaneous decorative and functional accessories — was looking to expand its cabinet portfolio and had experienced manufacturing challenges such as increased production lead-time. In an effort to improve operational performance and reduce costs, the facility reached out to the Tacoma-Pierce County Economic Development Board, who in turn brought in the state’s manufacturing extension partner, Impact Washington, and Ecology’s Lean/Green program.
Lean/Green is a customized service offered to Washington manufacturers in which continuous improvement principles and environmental methods are applied to help decrease operating costs and reduce environmental and energy impacts.
This public-private partnership received $100,000 from the State Job Skills Program and $25,000 from Lean/Green. The process improvements focused on:
- Manufacturing efficiency training for staff.
- Identifying and purchasing more effective equipment.
- Recycling and reuse of certain materials.
- Improved air compressor use.
- Installation of LED lighting.
- Methods to help improve and refine the manufacturing process.
Even as the company continued to expand its cabinet lines while adopting these process changes, the associated operational cost savings increased, while the dangerous waste, VOC air emissions, and energy use decreased (specific activity improvements and the projected results are shown in the table below). Founder’s Choice is now implementing recommendations and are on track to achieve:
- $112,000 in annual cost savings.
- 7,000 pound annual reduction in hazardous waste generated.
- 20% reduction in Volatile Organic Compounds (VOC) air emissions.
We're looking for projects in 2021
Ecology and Impact Washington are looking for businesses interested in 2021 projects. To find out more about these grant opportunities, please contact:
Hugh O’Neill
hugh.oneill@ecy.wa.gov
360-407-6354
Improvement activities
Process Category |
Process |
Estimated Reductions |
---|---|---|
Finishing Process Improvements |
Paint Spray Efficiency training for 5 staffs through the Pacific Northwest Pollution Prevention Resource Center. |
|
Purchase and install plural component spray guns to mix paint and catalyst at the point of application. |
|
|
Waste Management |
Purchase and install gaskets for a solvent still to minimize vaporization of the recycled solvent. |
|
Flush catalyzed paint material in designated waste drums and recycling corresponding breakthrough solvent for reuse. |
|
|
Energy Efficiency |
Switch fixed-speed air compressor to variable frequency drive compressors to enable precise control of the speed of the motors that drive the compressor. |
|
Implement LED lights in finishing area. |
|
|
Product Work Flow Optimization |
Implementation of automated track conveyor to conveniently transport painted and stained cabinet parts. |
|
Development of individual paint and stain drying segment for the finished cabinet parts. |
|