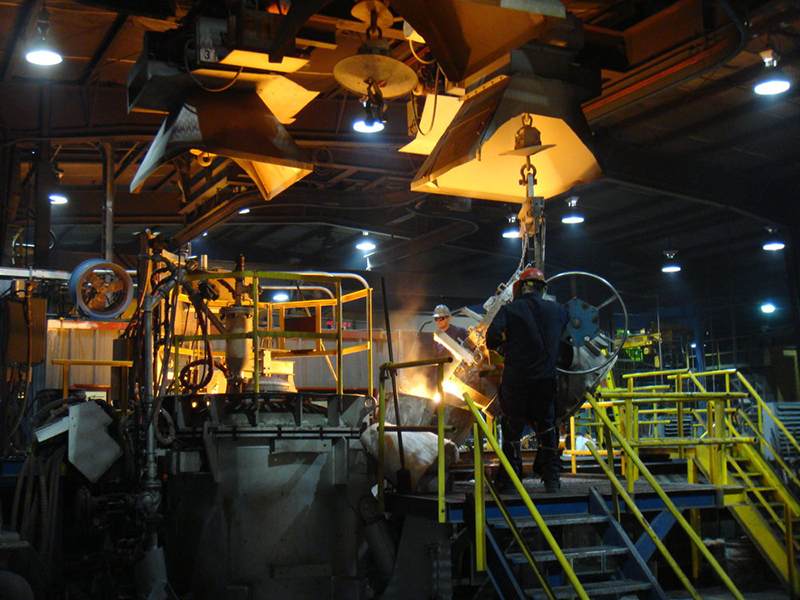
Romac Industries Inc. operates a steel fittings manufacturing facility in Bothell, Washington. As part of its production line, workers surface-finish stainless steel parts using a process called passivation, a chemical treatment for stainless steel and other alloys that helps treated surfaces resist corrosion. Unfortunately, this process generates about 32 tons of waste annually, so Romac Industries decided to find a better way.
That’s when they called Ecology’s Lean/Green program, a customized service offered to Washington manufacturers in which continuous improvement principles and environmental methods are applied to help decrease operating costs and reduce environmental and energy impacts.
Between spring and fall of 2021, Romac Industries collaborated with Ecology, Impact Washington, and Lean Environmental Inc. (LEI) to train on lean and green principles. Their goal was to use Ecology grant funding to decrease waste generation, maintain product consistency, and increase the safety of their workers on the passivation line.
Romac’s stainless steel ammonium bifluoride passivation process initially involved a series of four immersion tanks, two immersion rinses, and a high-pressure rinse that generated spent acid waste containing ammonia, fluorine, chromium and nickel. After LEI conferred with Romac about the nature of their waste streams and outlined a general approach for analysis and optimization, LEI (in partnership with Impact Washington) analyzed Romac’s passivation process with the goal of extending passivation tank life.
The Lean/Green training resulted in a project that produced real-world results. As the project progressed, it became obvious further modifications of the line could result in an almost complete elimination of the historical waste stream.
In the reengineered process, Romac set up a counter-current flow where acidic rinse tank water could circulate back into a process tank, effectively transferring reusable acidic plating solution back into the passivation process while ensuring rinse tank acid concentrations stayed low. This allowed process tank solutions to last longer and reduce the generation of spent acid waste.
Establishing counter-current flow was just the first step. Romac will be adding an ion exchange system to allow consistent water quality throughout the process and reduce waste by up to 50% more. The company continues to implement changes in 2022, with the goal of increasing from a one-tank rinse to four with the counter-current water flow, an automated rack transfer, and eventually an acid distillation system for product recovery and reuse.
Achievements to date
- About a 50% reduction in waste (64,000 to 30,000 lbs) the first year
- $50,000 per year in real savings
- Product quality improvement
- Greater process control
Upcoming changes will result in an estimated:
- 98% reduction in dangerous waste generation
- 200% increase in line capacity
- $100,000 per year in savings
- 50% reduction in labor costs
- Improved safety and ease-of-work procedures for operators
Thanks to their efforts, Romac has been awarded the MVP2 (most valuable pollution prevention) Multimedia Award by the National Pollution Prevention Roundtable. Since 1995, these awards have been used to recognize the very best in pollution prevention results and profile the many accomplishments by businesses to stop pollution before it’s even created.
To learn more about Ecology’s Toxic Reduction Assistance Program, please contact Toxics Reduction Specialist Paul Fabiniak at 425-457-3712 or paul.fabiniak@ecy.wa.gov.