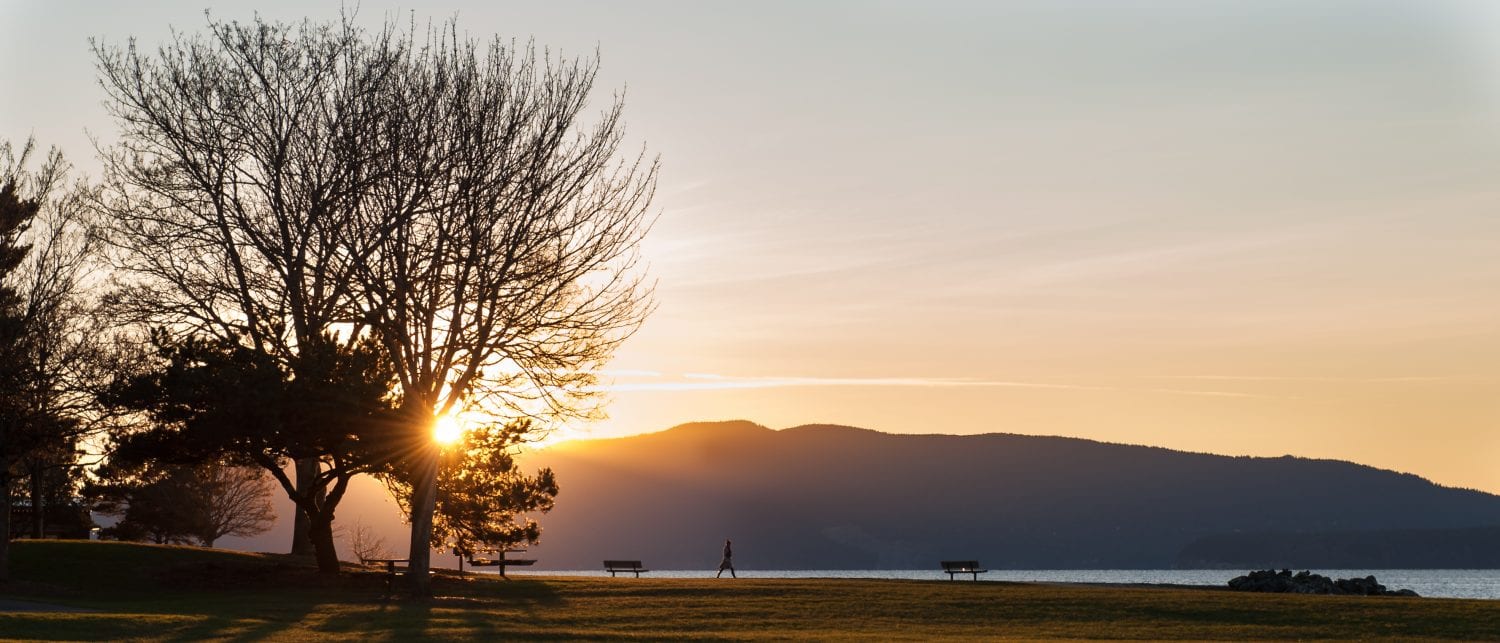
A portion of Boulevard Park on the Bellingham waterfront is also a cleanup site (Photo from City of Bellingham)
Have you ever taken a sunset stroll through Bellingham’s Boulevard Park? If so, you know firsthand why the community cherishes this waterfront park.
You may not have realized that the northern portion of the park is also the South State Street Manufactured Gas Plant cleanup site — so named for its industrial past.
This spring you’ll see environmental contractors collecting soil, groundwater, and sediment samples for testing to help inform cleanup of this area of the park.
How do you investigate a waterfront cleanup site that’s also a city park?
Boulevard Park and South State Street MGP site, before the 2017 interim action
The City of Bellingham’s Parks and Recreation Department will also be sure to keep you informed on how to recreate safely at the park during this work. As needed, the city will fence off any work areas and display informational signs. You can view updates of park projects from their Boulevard Park webpage.
Since last summer, crews have been busy doing this type of fieldwork throughout Bellingham Bay. See our stories about our other waterfront cleanup sites: I & J Waterway, Whatcom Waterway, and Central Waterfront.
Where is this site in the cleanup process? And what happens next?
Steps in Washington's formal cleanup process.
The planned fieldwork, called a pre-remedial design investigation, will provide additional information to complete engineering design of the final cleanup action.
The City of Bellingham and Puget Sound Energy (PSE) are conducting this fieldwork in accordance with an Agreed Order with Ecology.
Engineering design and permitting for cleanup will take about two years to complete, with construction work expected as early as 2023. The cleanup work will include a combination of removing structures, capping contaminated soil and sediment, enhancing the natural breakdown of groundwater contamination, protecting the shoreline, monitoring conditions, and restricting activities that could disturb capped areas.
What happened here?
Manufactured gas plant operations on hillside and log booms in Bellingham Bay, about 1955.
The city and PSE are cleaning up contamination from these historical industrial uses.
What will I see happening on the Bellingham waterfront?
Investigating soil and groundwater
A direct-push drill rig.
To better design the groundwater contamination cleanup, crews will gather more information from under ground. A direct-push drill rig will be used to determine subsurface conditions and to collect groundwater samples along the bluff and railroad tracks. Four new groundwater monitoring wells will be installed using hollow-stem auger equipment (two uphill from the pocket beach and two along the western shoreline.) Crews will also conduct two site-wide groundwater monitoring events using 21 wells during the wet season (April - May) and again in the dry season (July – September).
Check out the figures in the pre-remedial design investigation for sampling location maps.
Investigating sediment
The cleanup action for the marine area also calls for a clean cap. Since this will be underwater on the seafloor of Bellingham Bay, the design and investigation looks different from the upland areas.
The cap not only needs to isolate contaminated sediment, but in certain areas of the site it may also need to treat contaminated groundwater before the groundwater discharges to Bellingham Bay. This depends in part on how fast groundwater travels.
Example of fluorescent dye testing.
Crews will also sample nearshore intertidal sediment and porewater (water contained within the sediment) in 12 locations using hand-held coring and probing equipment. And yes, this could look as cool as it sounds! For this site, contractors will see the dye at the sediment surface (at low tide) and the picture to the right is just an example.
The tracer dying and the nearshore sampling will help inform the design of nearshore sediment capping.
To design the cap for sediment further from shore, crews will take 17 Power Grab and eight vibracore samples from marine research vessels. A Power Grab sampler collects or “grabs” shallow surface sediment, and a vibracore is a hollow tube that’s vibrated into the sediment to collect a continuous sediment sample across varying depths.
Power Grab sediment testing.
To evaluate how the seafloor sediment has changed over time and best design the sediment cap, crews will map the seafloor using multibeam sonar scanners from a marine research vessel.
Investigating coastal marine processes
Bellingham Bay wave model from Cornwall Avenue Landfill engineering design. The South State Street MGP site is on the waterfront at the bottom/center.
Engineers will also assess their design with other coastal concerns such as sea level rise, tides, storm surges, tsunamis, and local wind and wave conditions. They will build off what we’ve already learned from engineering other Bellingham Bay cleanups. They will also apply the most recent city and state guidelines and best available science to design a cleanup resilient to these marine forces.
Funding
Pre-remedial design investigation activities, including data evaluation and reporting, are expected to cost $700,000. The city and PSE are funding partners for the cleanup. The city is eligible for reimbursement of up to half of their cost from us through the state’s Remedial Action Grant Program, which helps pay for the cleanup of publicly-owned sites. The Legislature funds the grant program with revenues from a tax on hazardous substances
Cleaning up Bellingham Bay
The South State Street Manufactured Gas Plant site is one of 12 Bellingham Bay cleanup sites coordinated through the Bellingham Bay Demonstration Pilot. The pilot is a bay-wide multi-agency effort to clean up contaminated sediment, control sources of sediment contamination, and restore habitat, with consideration for land and water uses. In 2000, participants in this initiative developed the Bellingham Bay Comprehensive Strategy.