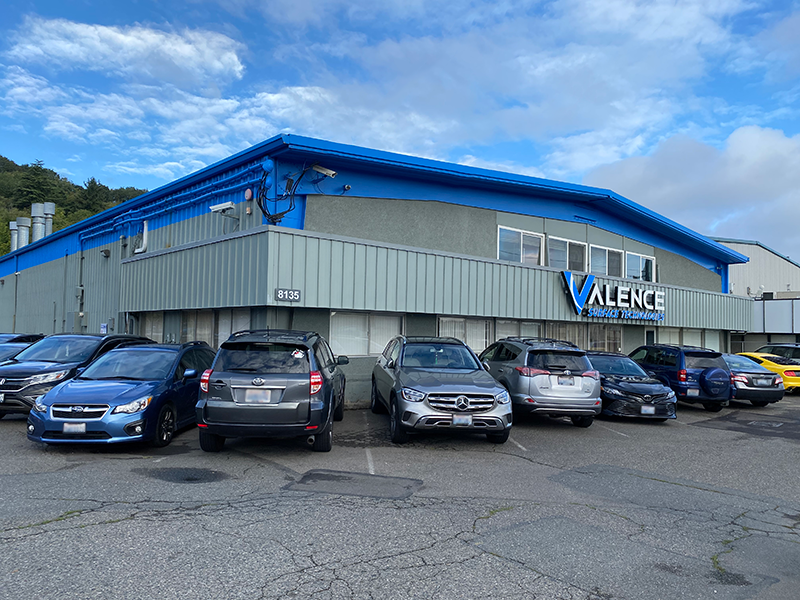
The Pollution Prevention Resource Center (PPRC) recently collaborated with us to help Valence Surface Technologies (also known as MAPSCO) to stop using a toxic chemical in their vapor degreasing operation.
MAPSCO, an aerospace surface finishing company that cleans, inspects, surface treats, and paints aerospace components, was using a chemical called 1-bromopropane (1-BP), which — according to an August 2020 risk evaluation by the Environmental Protection Agency — can carry unreasonable cancer, reproductive, and neurological human health risk.
Between January 2019 and September 2020, MAPSCO worked closely with PPRC to review specifications, better understand contaminants in their processes, adopt less toxic cleaning alternatives, and improve energy efficiency.
MAPSCO purchased and installed a RAM Equipment aqueous-based cleaning system.
MAPSCO’s efforts to eliminating hazardous cleaning chemicals stemmed from an interest in decreasing worker exposure during cleaning practices and a desire to eliminate use of hazardous chemicals. We helped connect the facilities with pollution prevention expertise, assisted with identifying safer alternative options, and ensured the company met regulatory requirements during the project. MAPSCO ended up adopting the safer alternative after going through cost analysis and performance testing.
- Reducing 8,050 pounds of 1-BP products.
- Reducing vapor degreasing waste by 2,800 pounds per year.
- Additional $5,600 cost per year in increased labor for aqueous cleaning operations (labor to operate equipment remained the same, although labor costs increased by 20% over the project due to increased number of parts being cleaned using the new system).
- Saving $21,100 in chemical purchases per year.
- Saving $2,000 in waste disposal costs per year.
- Two year return on investment.
- Reducing energy usage by 50,000 kilowatt-hour (kwh) per year.
- Saving $8,000 in energy utilities.
- Reducing cleanup time by 10%.
- Improving paint job accuracy and preventing on-job mistakes.
MAPSCO Vice President of Environmental Health and Safety, Cory McGraw, says "The degreaser replacement project has worked out very well, and that this success story inspired a similar project at their site in West Springfield, Massachusetts."
Aerospace parts cleaning has been using halogenated chemicals like 1-BP in their cleaning operations for decades. 1-BP was once considered an alternative to other chemicals such as perchloroethylene (PERC), methylene chloride, and chlorofluorocarbons (CFCs). The industry is now working to develop ways to address these risks. Additionally, the EPA added 1-BP to the list of hazardous air pollutants under the Clean Air Act, further restricting use of the chemical.
If you have questions, contact the PPRC's Katy Wolf, PhD, at katywolfirta@gmail.com or 818-371-9260. To learn more about our toxics reduction efforts, contact Robert Reuter at robert.reuter@ecy.wa.gov or 425-457-3274.